Blog Tutto quello che devi sapere sul mondo delle fusioni di alluminio
8 Articoli
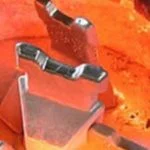
Nella realizzazione di fusioni in lega di alluminio con la tecnologia della sabbia a verde, meglio conosciuta come “fusioni in terra”, i forni ricoprono un ruolo chiave in termini qualitativi e quantitativi della lega ottenuta. In questo articolo elencherò, in maniera generica, le varie tipologie di forni che…
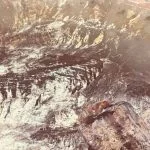
Nella realizzazione di fusioni in alluminio la corretta gestione della lega, durante i processi fusori e di mantenimento, riveste un punto chiave per il raggiungimento della qualità finale dei getti. Ormai da diversi anni il mercato richiede fusioni in lega di alluminio dalle elevate qualità per le varie…
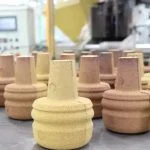
Le anime da fonderia sono particolari oggetti prodotti in materiale refrattario, solitamente sabbia silicea o quarzifera con l’aggiunta di leganti, cioè miscele chimiche che aderiscono ai grani per fornire resistenza meccanica all’anima. Le anime da fonderia servono ad ottenere cavità, fori o forme particolari come cave o rientranze,…
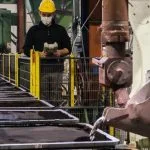
Le fusioni in alluminio in terra presentano molti vantaggi rispetto ad altre tecnologie di produzione. Colata in terra e pressofusione: differenze La fusione in alluminio in terra ha saputo mantenere nel corso dei secoli il ruolo di leader incontrastato in alcuni settori ed è alla base…
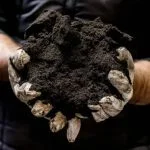
La terra da fonderia ricopre un ruolo fondamentale nella realizzazione e nella sanità delle fusioni in alluminio in sabbia a verde. Cos’è la terra da fonderia? Durante il processo produttivo delle fusioni in sabbia a verde, più comunemente chiamate fusioni in terra, la terra o sabbia di…
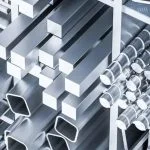
La storia dell’alluminio L’alluminio viene identificato per la prima volta nel 1807 nell’allume dallo scienziato inglese Humphry Davy, che ipotizzò che l’”alum” fosse il sale di un metallo ancora sconosciuto a cui diede il nome di “alumium”, successivamente modificato in “aluminium”. Solo nel 1825 il fisico danese Hans…
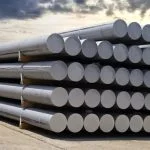
Le leghe di alluminio non sono tutte uguali, in base ai tipi di alluminio scopriamo insieme le caratteristiche meccaniche, chimiche e fisiche. Le leghe di alluminio Tra i principali scopi dell’uomo c’è la continua ricerca di produttività e funzionalità spingendolo sempre più nello studio, nella progettazione e nella…
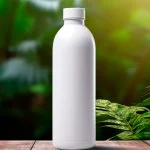
Prima di parlare dell’alluminio verde è necessario considerare le conseguenze sull’ambiente della produzione dell’alluminio primario. Il riscaldamento climatico globale è diventato ormai da alcuni anni il principale nemico del pianeta e dell’umanità. La temperatura terrestre ha visto un aumento pari a 0,7°C rispetto all’era pre-industriale. Proseguendo…