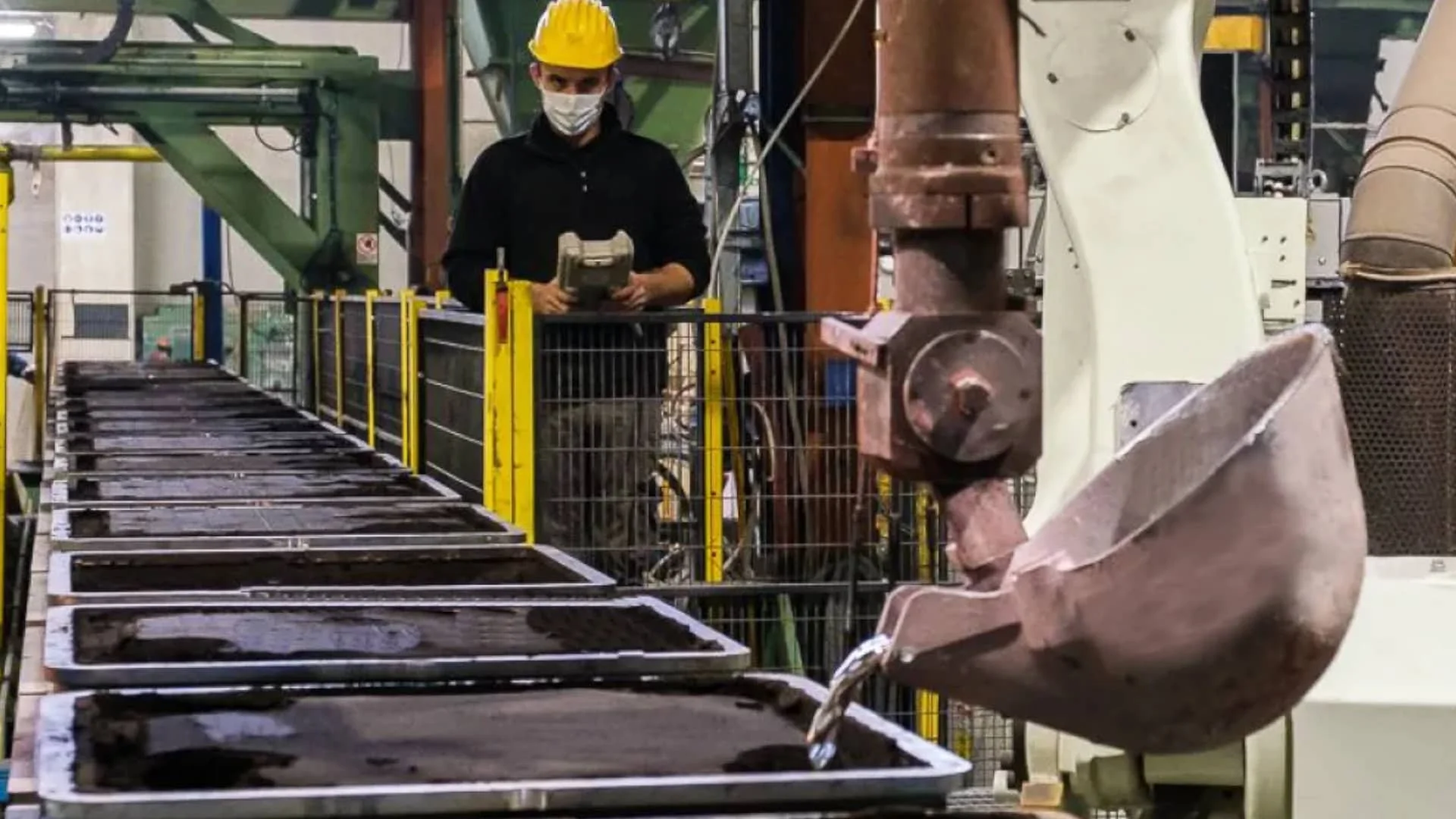
Le fusioni in alluminio in terra presentano molti vantaggi rispetto ad altre tecnologie di produzione.
Colata in terra e pressofusione: differenze
La fusione in alluminio in terra ha saputo mantenere nel corso dei secoli il ruolo di leader incontrastato in alcuni settori ed è alla base di molteplici progetti di sviluppo in svariati settori produttivi.
Oggi esistono anche altri processi di fonderia, ma per la giusta scelta bisogna conoscere i vantaggi e gli svantaggi della tecnologia prescelta al fine di ottenere fusioni di qualità con il corretto valore economico.
Esistono svariati “processi di colata”, ma tutti questi si possono suddividere in due macro-categorie:
Processi in forma transitoria: colata in terra o in sabbia a verde, Shell moulding, colata in polistirene espanso (schiuma persa), microfusione (cera persa), colata in gesso e colata in ceramica.
Vengono chiamati processi in forma transitoria in quanto la forma utilizzata per formare il pezzo viene distrutta al termine del processo per estrarre il pezzo. Il modello utilizzato per creare la forma viene riutilizzato infinite volte, è solo il negativo della forma che si vuol realizzare che viene distrutto.
Processi in forma permanente: Colata in conchiglia, colata in bassa pressione, Colata sotto vuoto, Pressofusione, Colata centrifuga.
Vengono chiamati in forma permanente perché la forma (in questo caso lo stampo) viene riutilizzata per numerosi cicli produttivi.
In questo articolo metteremo due tecnologie di fusione a confronto: la fusione in alluminio in terra (detta anche in sabbia a verde) e la pressofusione in alluminio.
Fusioni in alluminio in terra (o in sabbia a verde)
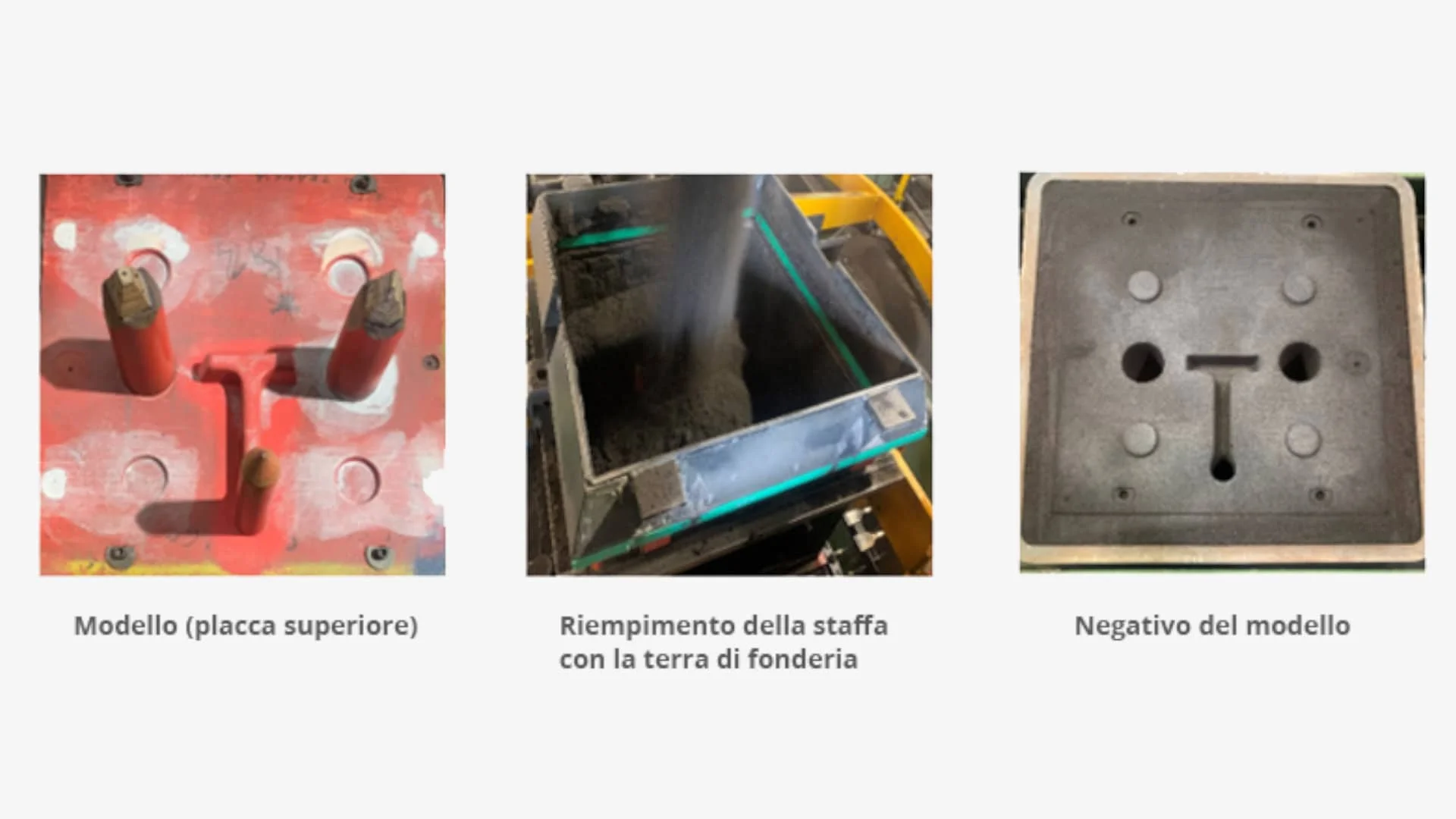
Quella della colata in terra è la classica e più antica lavorazione di fonderia.
Partendo dal modello, sempre diviso in due metà (mezza inferiore e mezza superiore) si produrrà un negativo di esso utilizzando una terra speciale, chiamata terra da fonderia.
Sopra al modello viene posta la staffa che è un contenitore per la terra da fonderia che consente di pressare la terra senza che la forma si rovini durante l’intero processo di produzione.
Il metallo fuso viene colato nello stampo di terra che alla fine del processo, quando si sarà solidificato, verrà distrutto per estrarre il pezzo.
Il modello può essere costruito in diversi materiali come: legno, resina o alluminio. Oggi il materiale più utilizzato è la resina a media o alta densità. Il modello può essere utilizzato per produrre migliaia di forme in terra.
Processo di produzione delle fusioni in alluminio in terra
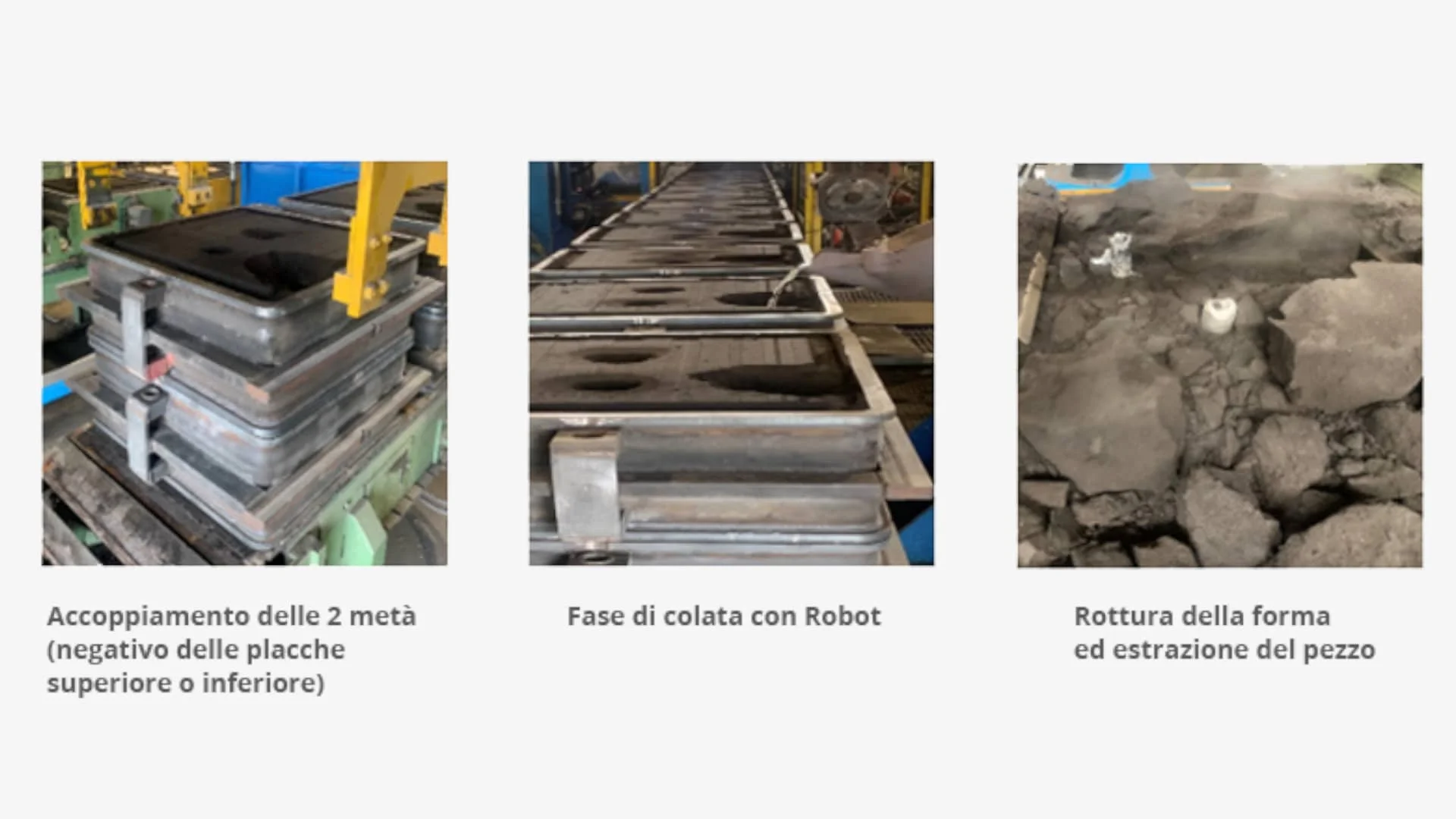
È uno dei processi dotati di maggiore versatilità e può essere realizzato praticamente con ogni tipo di metallo o lega.
La gamma di pezzi ottenibili tramite processi di fonderia può variare molto: da oggetti più piccoli e di geometria decisamente semplice, come lingotti, a prodotti decisamente più ingombranti e di elevata complessità, come motori navali.
Va precisato che in caso di oggetti particolarmente complessi e ingombranti, la scelta di realizzazione tramite fonderia è praticamente “obbligata”.
Possiamo così sintetizzare i vantaggi della fusione in alluminio in terra:
- Versatilità di produzione
- Possibilità di produrre forme complesse
- Possibilità di utilizzo di leghe differenti
- Economicità del modello
Fusioni in alluminio in pressofusione
La colata in pressofusione, conosciuta anche come colata in pressione, è un metodo di colata che prevede il versamento dell’alluminio liquido in una camera a pressione per riempire la forma (detta anche stampo) ad alta velocità.
Il metallo, tenuto a una temperatura poco più alta di quella di fusione, viene spinto e pressato dal pistone nella forma metallica dove solidifica rapidamente.
Il liquido metallico viene “pressato” nella cavità ad alta velocità ed in tempi brevi, per alcuni pezzi meno di anche meno di 5 secondi, è pronto per essere estratto il pezzo.
La forma metallica, chiamata anche stampo, è costruita perlopiù in ghisa o in acciaio. Questa è suddivisa in due metà che verranno a chiudersi sotto l’impulso della macchina creando lo stampo completo che andrà sottopressione.
Forma o “stampo” per pressofusione
La tecnologia della pressofusione dei metalli inizia la sua storia nella seconda metà dell’Ottocento negli Stati Uniti d’America. Da allora questo processo produttivo ha raggiunto notevoli processi tecnologici.
Esistono due tipologie di macchine per pressofusione:
1) Camera calda: il serbatoio contenente il metallo fuso si trova all’interno di una fornace funzionante. Garantisce produzioni elevate e maggior qualità (visto il rapido prelievo dal serbatoio) in quanto il metallo fuso si presenta con una composizione più omogenea.
2) Camera fredda: il metallo è fuso in un forno vicino alla macchina, caricato nella camera fredda manualmente o tramite robot pronto per essere iniettato nello stampo. La macchina a camera fredda ha un tempo di raffreddamento minore della fusione, quindi un ciclo più veloce.
La pressofusione consente di ottenere fusioni molto precise. Nella maggior parte dei casi le parti pressofuse possono essere utilizzate direttamente per l’assemblaggio senza ulteriori lavorazioni meccaniche.
I vantaggi della pressofusione
- Ottima finitura superficiale
- Eccellente precisione dimensionale
- La riduzione delle porosità e delle impurità
- La precisione degli spessori soprattutto sottili
- Raffreddamento rapido, che conferisce una granulometria fine e buone proprietà meccaniche al pezzo
- Maggior velocità di produzione
Gli svantaggi della pressofusione
- Limitazione nella geometria del componente, che deve essere estratto con facilità dallo stampo
- Costo elevato dello stampo, da armonizzare con grandissime serie
- Ridotto numero di leghe di alluminio utilizzabili